Accélérer l'innovation avec la fabrication additive
Percées réalisées en quelques semaines
Yohann Rousselet : directeur mondial, Innovation technologique chez Baltimore Aircoil Company, Inc.
Le prototypage rapide et itératif avec fabrication additive (également connue sous le nom d'impression 3D), lorsqu'il est utilisé dans le cadre d'un processus d'innovation méthodique, réduit considérablement le délai de commercialisation des nouveaux produits. La rapidité et le faible coût du prototypage rapide avec la fabrication additive permettent de concevoir et de tester de nombreuses versions, de comparer rapidement des conceptions alternatives et d'améliorer et d'affiner de manière itérative les conceptions.
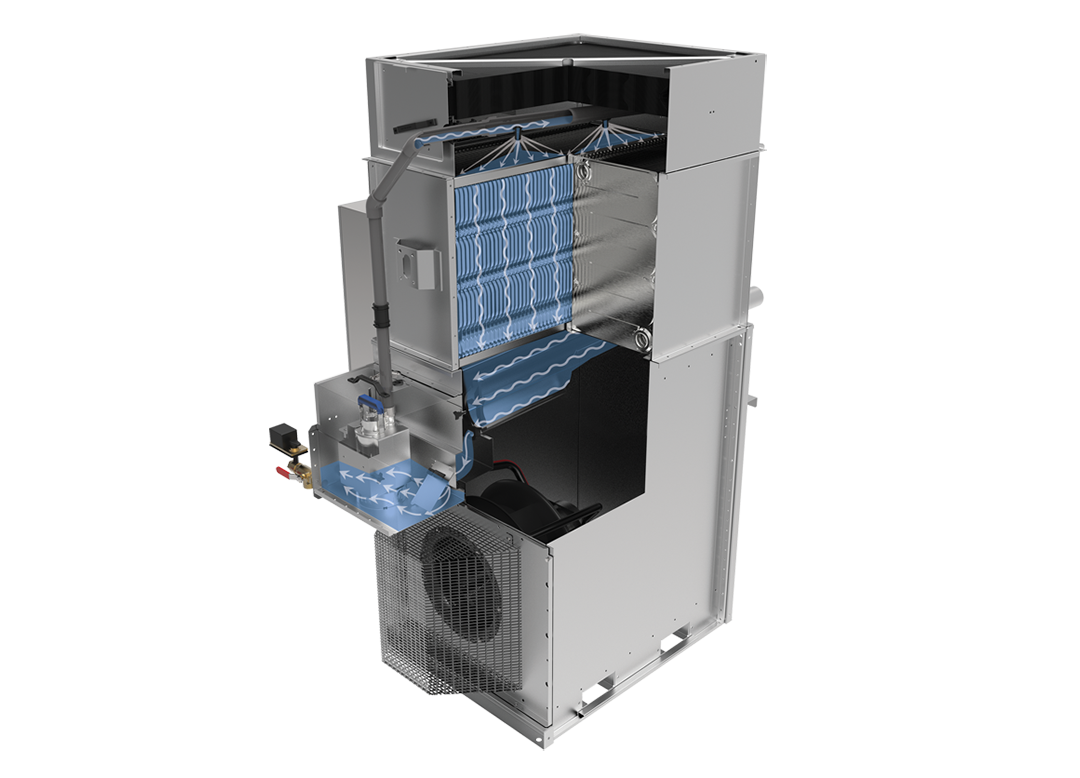
Nouveau produit révolutionnaire
Baltimore Aircoil Company (BAC) a utilisé la fabrication additive pour développer le refroidisseur hybride modulaire Nexus®, un grand pas en avant dans les systèmes de refroidissement de fluides hybrides pour les applications CVC et industrielles légères.
L'une des principales caractéristiques de conception du Nexus Cooler est la conception brevetée DiamondClear®, qui permet un auto-nettoyage continu, réduisant considérablement les coûts d'entretien du bassin d'eau et réduisant le volume d'eau de pulvérisation jusqu'à 60 %. Cela peut également aider à éliminer le besoin de traitement traditionnel de l'eau.
Cette performance inégalée résulte des innovations dans la conception de deux composants essentiels du DiamondClear® Design :
Système de collecte d'eau en pente - L'eau à grande vitesse qui coule efficacement sur les gouttières et les embouts réduit l'accumulation de tartre et la croissance biologique.
Buses de pulvérisation sous pression optimisées - Une distribution uniforme de l'eau sur l'échangeur de chaleur maximise les performances.
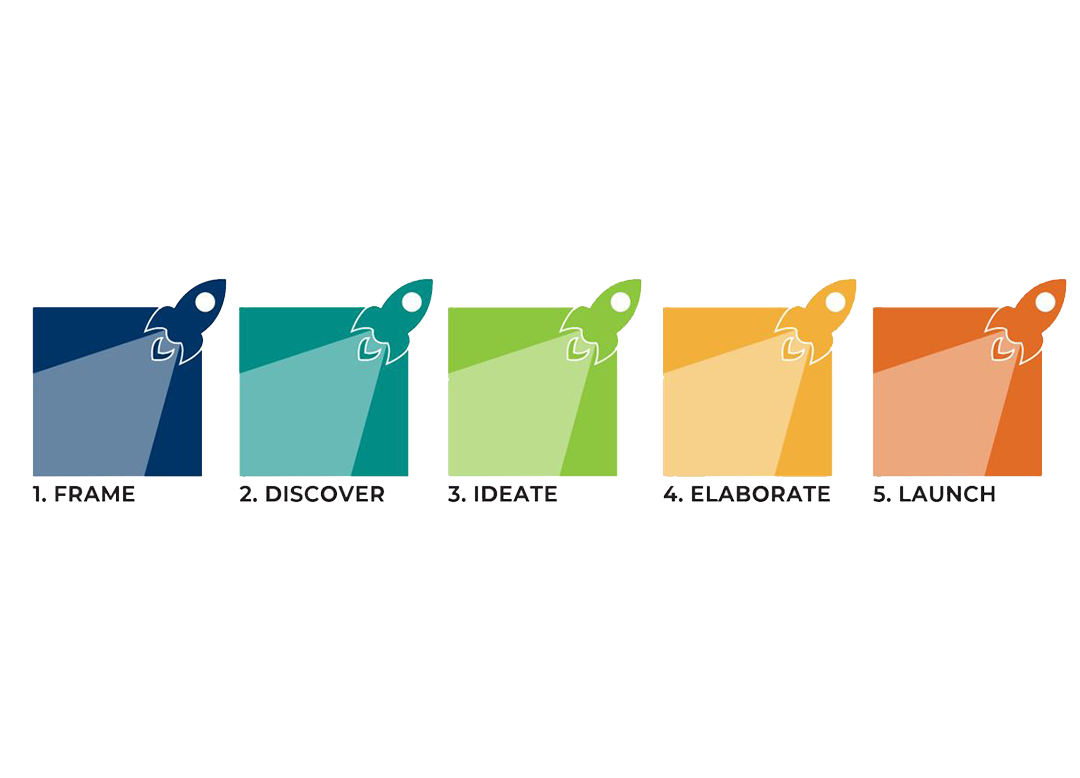
Processus d'innovation rapide
BAC et toutes les unités commerciales de la société mère de BAC, Amsted Industries, utilisent un processus d'innovation rapide en cinq étapes. Les trois premières étapes - opportunités de marché FRAME, DISCOVER des informations critiques et IDEATE concepts révolutionnaires - informent et guident les étapes suivantes.
La quatrième étape - ÉLABORER des prototypes rapides - utilise la fabrication additive parmi d'autres outils dans un processus itératif de création de plusieurs versions et d'exploration et d'évaluation d'alternatives majeures et d'améliorations précises.
L'étape finale - les solutions validées par LAUNCH - utilise des prototypes imprimés en 3D à grande échelle avec d'autres méthodes pour les tests finaux et la validation du concept.
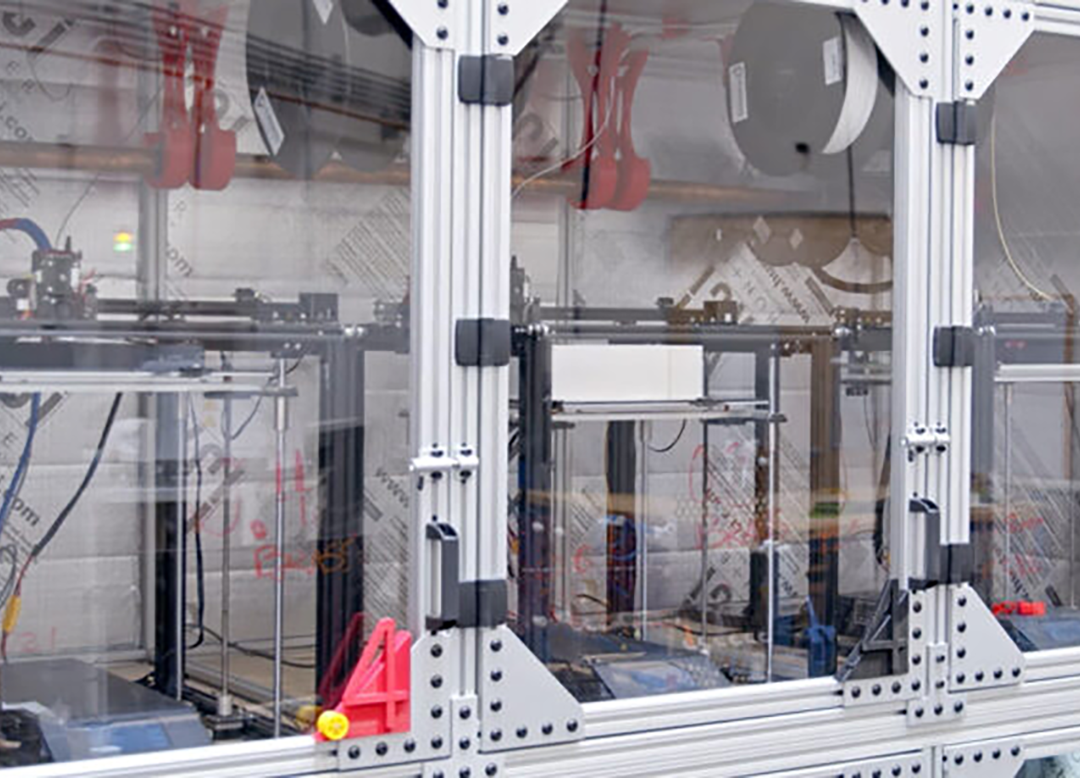
De l'idéation aux solutions validées en moins de 10 semaines
Au cours de l'étape ELABORATE, la gouttière des prototypes de système de collecte d'eau en pente a été imprimée en 3D en interne, ce qui a permis à l'équipe d'évaluer rapidement les capacités de gestion de l'eau de cinq conceptions différentes. Ces tests, combinés à une analyse CFD (dynamique des fluides computationnelle) détaillée du comportement aérodynamique de plusieurs conceptions des profils de gouttière, ont donné à l'équipe la confiance nécessaire pour aller de l'avant avec la conception sélectionnée.
Pour l'étape de LANCEMENT, BAC a acheté une imprimante 3D plus grande pour répondre aux capacités de volume de construction pour effectuer des tests à grande échelle, et le retour sur investissement a été réalisé en moins de 6 mois. Le développement du premier prototype de système de collecte d'eau à grande échelle a été achevé en moins de 10 semaines, de l'idéation aux tests de validation du premier prototype à grande échelle. Les conceptions de production finales comprenaient à la fois des pièces moulées par injection et extrudées.
De plus, la fabrication additive a permis à l'équipe de réduire le temps de développement des buses de pulvérisation de 9 mois à 6 semaines. L'impression 3D sur site a réduit le délai de production du prototype de buse de 2 à 4 semaines à moins de 24 heures, ce qui a considérablement raccourci la durée du processus de conception itératif. Les pièces de production finales ont été moulées par injection.
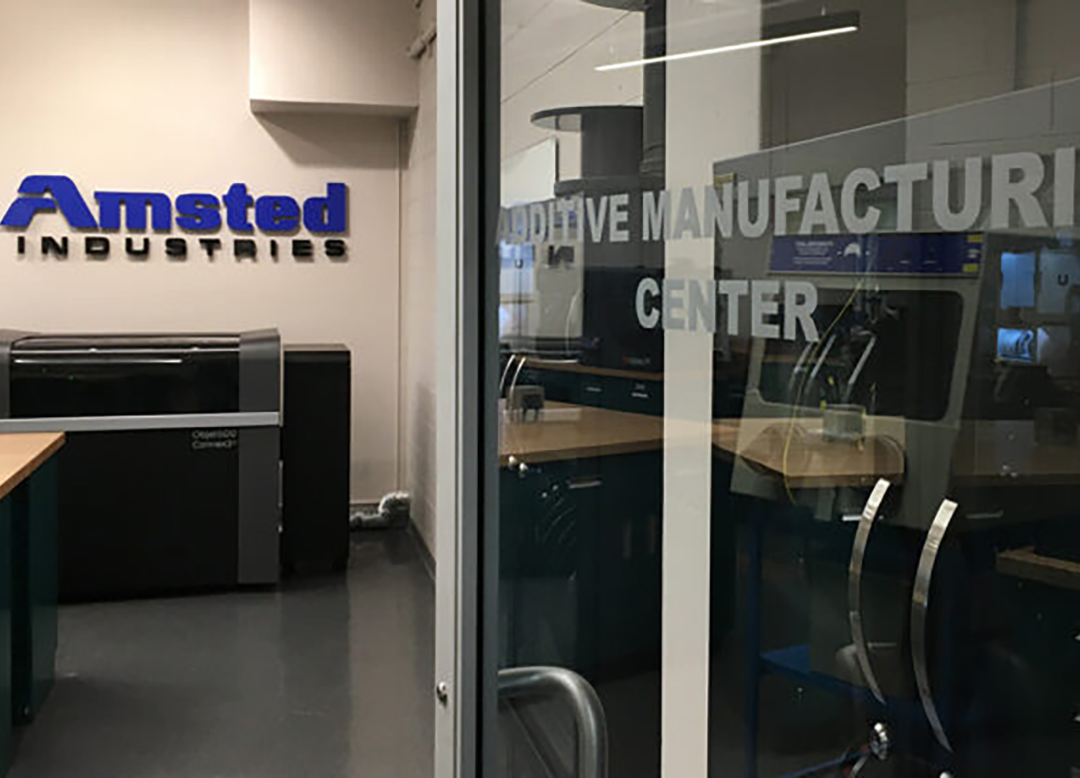
Accélérer l'innovation
La capacité de fabrication additive en interne est essentielle pour contrôler la qualité, les délais et les coûts. Le prototypage rapide avec la fabrication additive donne aux concepteurs et aux ingénieurs plus de liberté pour explorer des solutions créatives et tester des concepts avec une analyse empirique, ce qui donne des produits aux performances révolutionnaires.
Avec le succès de BAC avec le refroidisseur hybride modulaire Nexus® et les produits ultérieurs, combiné au succès d'autres unités commerciales d'Amsted avec la fabrication additive, la société mère de BAC, Amsted, a créé trois laboratoires de fabrication additive partagés qui dépassent les capacités de chaque entreprise.