Remplacement des tours érigées sur site par des tours modulaires : une solution plus sûre et plus rapide pour Toyota
Par Stephen G. Kline, PE, MBA, directeur technique mondial – secteurs verticaux à forte croissance, Baltimore Aircoil Company
Comment remplacer les tours de refroidissement vieillissantes sans risquer de perturber le fonctionnement continu à haut volume d'une usine ? C'était le défi de l'usine Toyota de Princeton, dans l'Indiana. La camionnette Toyota Tundra a commencé à sortir des chaînes de production en 1998 dans une installation de 4,5 millions de pieds carrés (environ 80 terrains de football sous un même toit), et les tours de refroidissement existantes devaient être remplacées.
Le remplacement de la tour de refroidissement faisait partie d'un projet de modernisation de l'usine de 1,3 milliard de dollars qui comprenait le réoutillage, de nouveaux équipements et des technologies de fabrication avancées, augmentant la capacité à 420 000 véhicules par an pour répondre à la forte demande, principalement pour les véhicules hybrides populaires de l'entreprise.
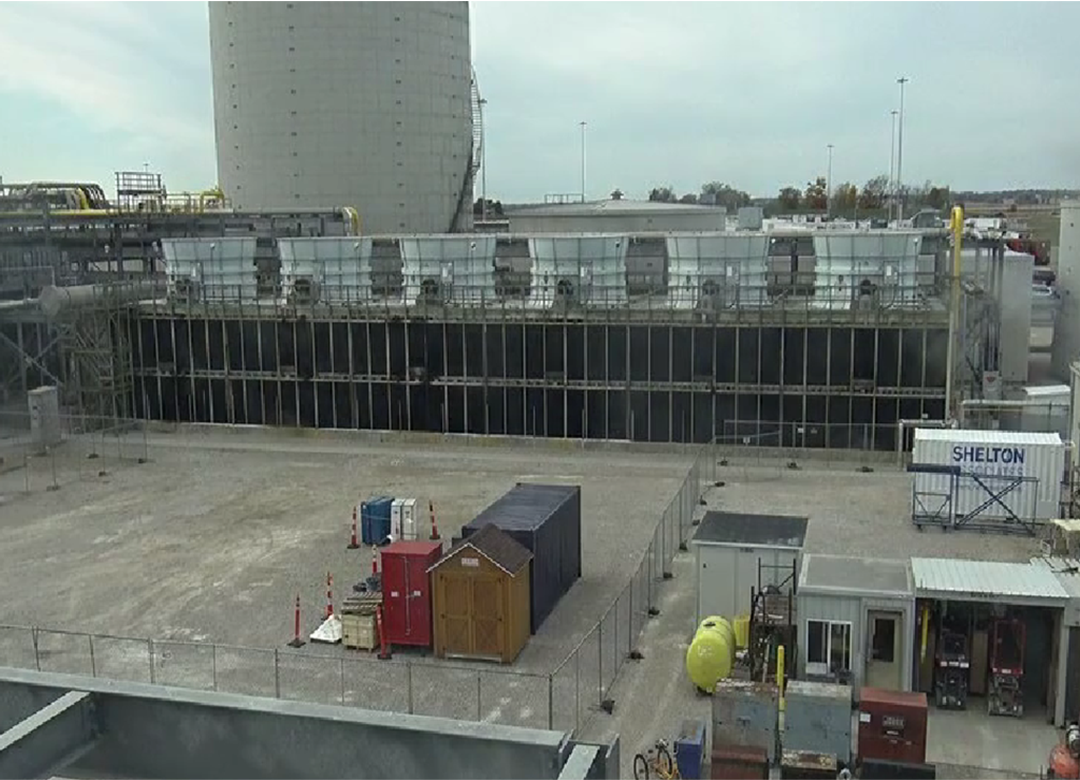
Avant : Les tours existantes érigées sur le terrain doivent être remplacées.
Le défi
Le remplacement des énormes tours de refroidissement érigées sur le terrain n'était pas une mince affaire et devait être achevé dans un délai limité, lorsque le refroidissement n'était pas nécessaire, afin d'éviter de provoquer un arrêt des opérations de l'usine. La démolition n'a pu commencer qu'en décembre et la préparation du site, l'installation et la mise en service du nouveau système devaient être achevées d'ici avril.
Toyota a travaillé avec Ryan Halvorsen chez ElitAire LLC. évaluer les alternatives technologiques et élaborer un plan. La première décision à prendre concernait la méthode de construction : remplacer les tours érigées sur site non-BAC existantes par un système similaire construit sur site ou installer un système modulaire construit hors site dans l'usine de BAC. La deuxième décision concernait la technologie d'entraînement des ventilateurs : continuer à utiliser un système d'entraînement par engrenages ou passer à la technologie d'entraînement direct.
L'objectif principal de Toyota était de contrôler les risques, le risque de retards dans le processus d'installation pouvant entraîner un arrêt de la production, ainsi que le risque pour la sécurité des travailleurs, ce qui était d'une importance capitale. L'équipe d'approvisionnement recherchait également une solution économe en énergie et nécessitant peu d'entretien afin de réduire les coûts et l'impact environnemental.
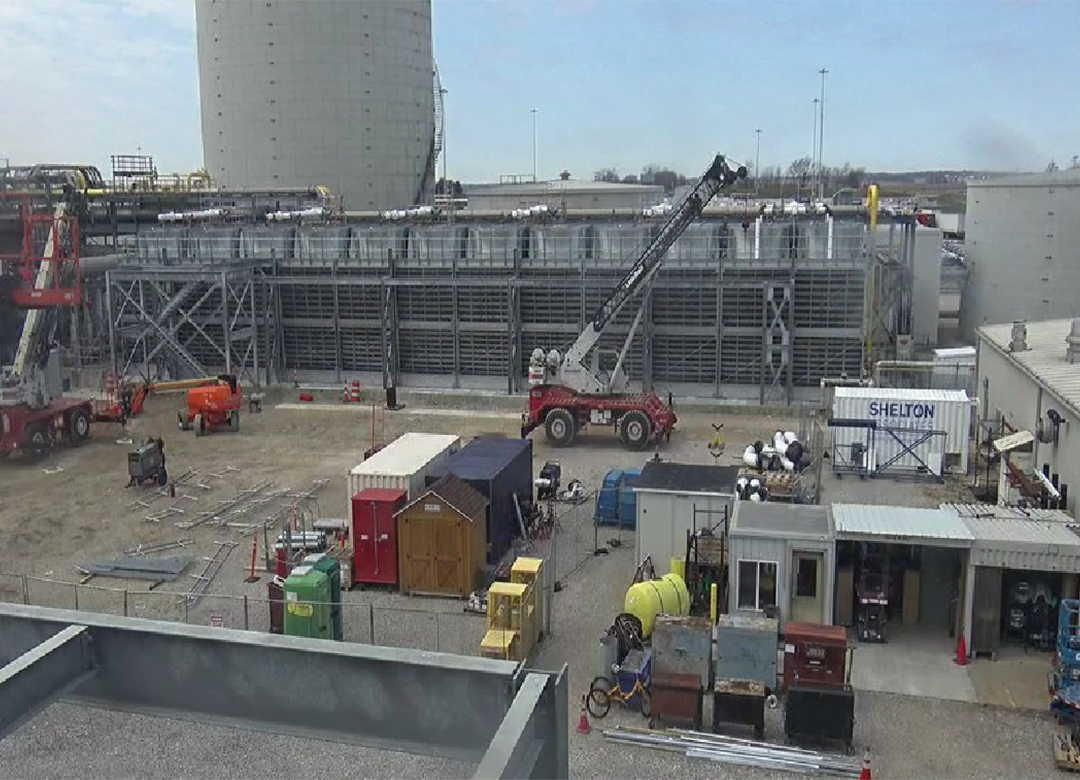
Après : Les modules BAC série 3000 ont été installés en seulement quatre jours, contre deux à trois mois nécessaires pour assembler des tours de refroidissement montées sur site.
Le système modulaire réduit les risques
Après avoir évalué les coûts du cycle de vie et pesé les risques de diverses alternatives, Toyota a sélectionné la tour de refroidissement modulaire série 3000 de BAC avec le système de ventilateur ENDURADRIVE® à entraînement direct. Bien que Toyota ait déjà installé deux modules de série 3000 dans une usine différente, ce projet à Princeton, dans l'Indiana, était différent à deux égards. Premièrement, ce projet était d’une ampleur nettement plus grande. Deuxièmement, alors que le projet précédent était une nouvelle installation, le projet actuel impliquait des unités de remplacement utilisant le bassin d'eau froide en béton existant. Ces différences, associées aux contraintes de temps, ont ajouté à la complexité et aux risques.
Compte tenu de ces facteurs, la tour de refroidissement série 3000 de BAC était la solution idéale. Toyota a pu remplacer les (6) tours érigées sur le terrain par (12) tours de refroidissement modulaires de la série 3000 tout en réutilisant le bassin d'eau froide en béton existant.
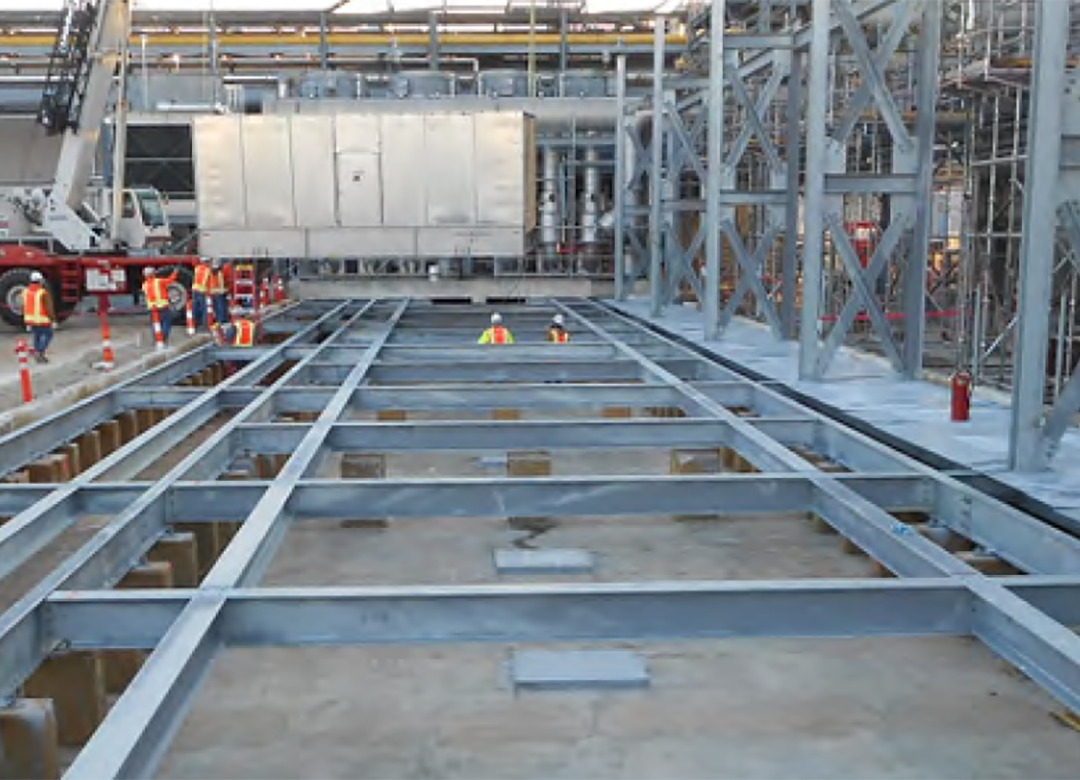
Les modules BAC Série 3000 ont été installés sur le bassin d'eau froide en béton existant.
Un facteur clé dans la décision de Toyota a été le temps d'installation. Remarquablement, l'entreprise de construction mécanique Harrell-Fish Inc. (HFI) a pu installer la gamme complète des modules de la série 3000 en seulement quatre jours, comparativement aux plus de 60 jours qui auraient été nécessaires pour assembler un module de terrain. système érigé de même taille et capacité.
Comme l'a noté Hassan Alhashim, ingénieur de projet principal chez ElitAire : « Au lieu de prendre 2 à 3 mois pour ériger les tours construites sur site, les modules ont été installés chacun en 3 heures environ, et l'ensemble du processus, de la démolition à l'achèvement, a été accompli en un temps record. la fenêtre de quatre mois.
De plus, Toyota a pu effectuer des inspections visuelles et des tests d'acceptation en usine des modules de la série 3000 avant qu'ils ne quittent l'usine de BAC, plutôt que de s'appuyer sur le processus plus difficile et plus long consistant à effectuer ces tests sur site.
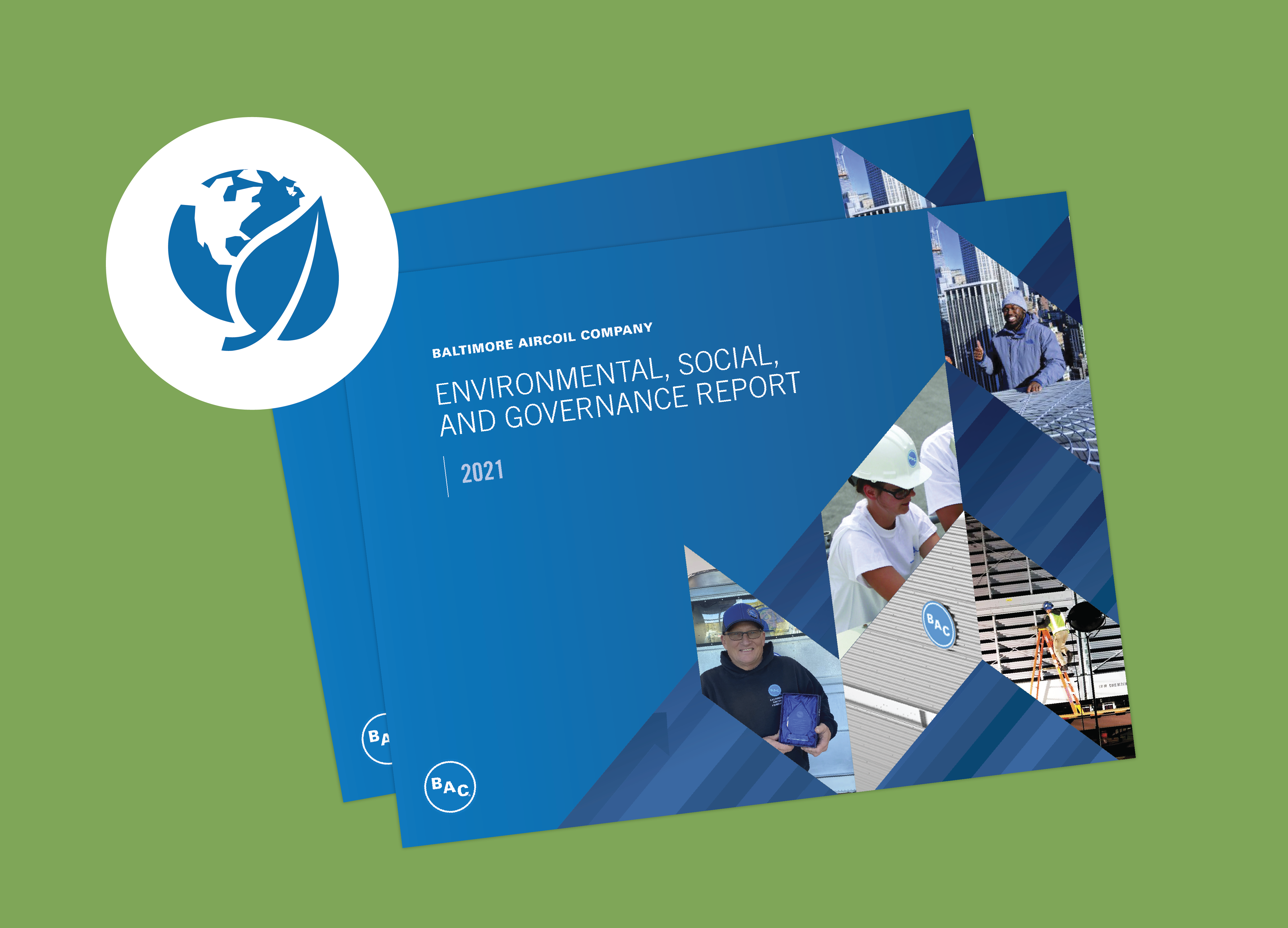
La compression du calendrier et la réduction des risques de retards inhérents aux projets de construction sur le terrain étaient d'une importance cruciale pour Toyota, tout comme la réduction des risques de sécurité, un élément central de leur culture d'entreprise. Les tours de refroidissement modulaires de BAC sont construites hors site dans les usines de BAC sous un contrôle de qualité strict et des normes EHS. Les tours modulaires sont expédiées sur le chantier une fois terminées en sections supérieure et inférieure avec un temps d'assemblage sur site minimal. L'utilisation de tours de refroidissement modulaires fabriquées en usine a réduit les risques de sécurité pour Toyota puisque l'usine n'a pas été un chantier de construction actif pendant plusieurs mois comme elle l'aurait été avec des tours érigées sur le terrain.
Apprenez-en davantage sur le programme de santé et de sécurité environnementales (EHS) de BAC en lisant le rapport environnemental, social et de gouvernance (ESG) de l'entreprise sur www.baltimoreaircoil.com/sustainability .
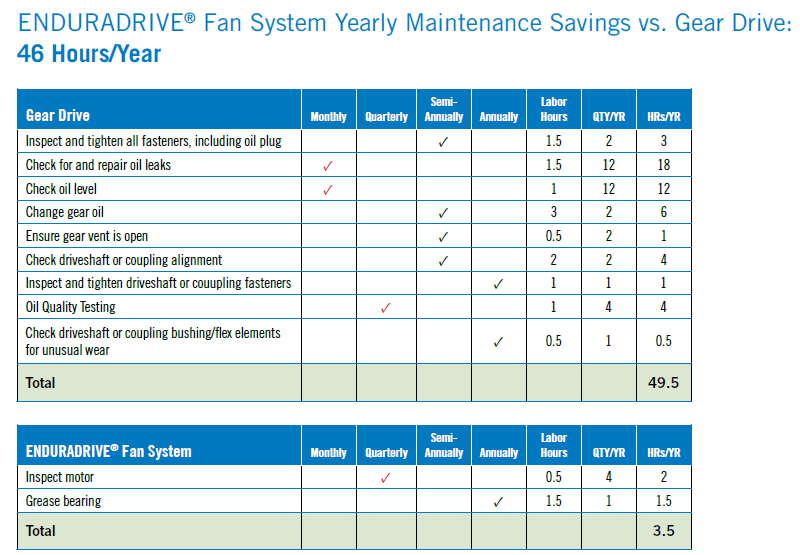
L'entraînement direct réduit les coûts et l'impact environnemental
Dans son ancien équipement, Toyota utilisait des systèmes d'entraînement par engrenages, mais a décidé de tirer parti du système de ventilateur ENDURADRIVE® à entraînement direct de BAC dans les nouvelles tours de refroidissement. Les conceptions à entraînement direct éliminent les pertes mécaniques et permettent ainsi d'économiser de l'énergie par rapport aux systèmes d'entraînement par engrenages et par courroie, réduisant ainsi les coûts et l'empreinte carbone. Les moteurs à entraînement direct utilisent une technologie à aimant permanent efficace et fiable et éliminent les dépenses et l'impact environnemental des vidanges d'huile.
Les systèmes d’entraînement par engrenages nécessitent beaucoup plus d’entretien, notamment des inspections de l’huile des engrenages et des vidanges d’huile régulières. Pour les usines de fabrication qui tiennent compte des règles OSHA relatives au travail dans des espaces confinés dans leurs décisions d'achat, les ventilateurs à entraînement direct nécessitent des interventions de maintenance beaucoup moins fréquentes. Toyota effectue sa propre maintenance en interne et en passant au système de ventilation ENDURADRIVE®, elle réalisera des dizaines de milliers de dollars d'économies opérationnelles annuelles et réduira considérablement les heures de maintenance planifiées, comme indiqué dans le tableau des calendriers de maintenance préventive.
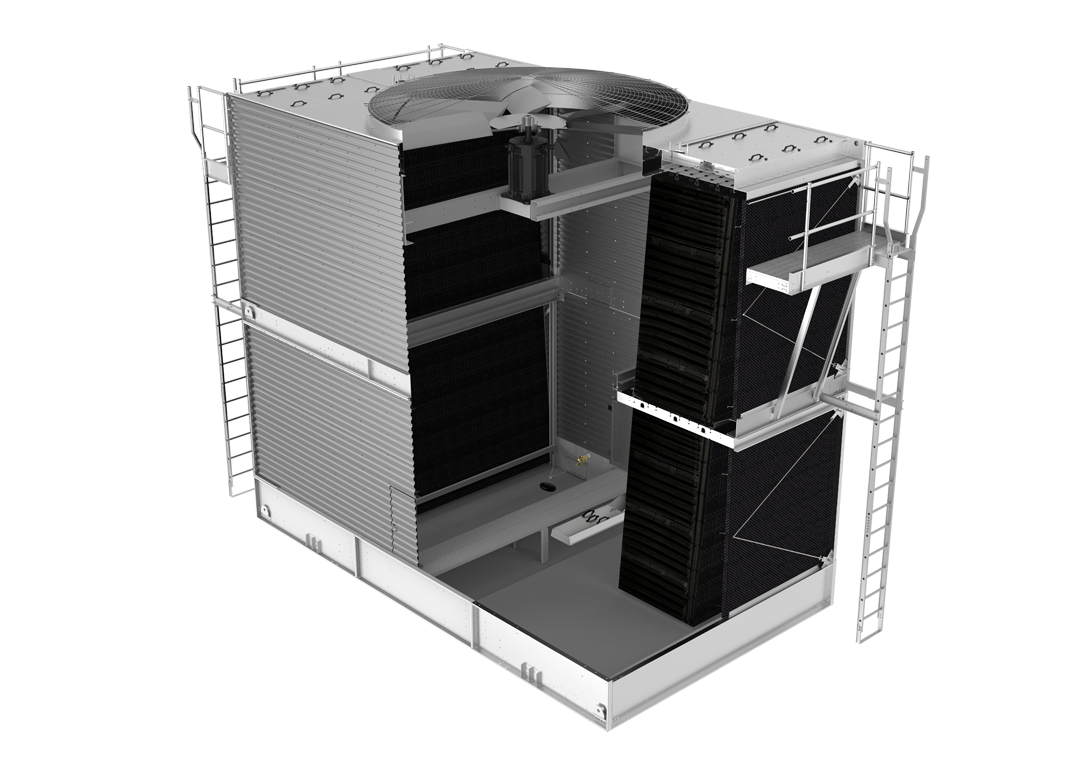
Conclusion : premier coût par rapport au coût total de possession
Les tours de refroidissement modulaires Toyota de BAC équipées du système de ventilation ENDURADRIVE® ont été installées dans les délais et dans les limites du budget et ont fonctionné de manière fiable tout en réduisant considérablement la maintenance. Depuis cette installation à l'usine de Princeton, Toyota a continué à installer des unités modulaires de la série 3000 sur d'autres sites aux États-Unis et a choisi BAC pour répondre à ses besoins de refroidissement.